Float Glass Manufacturing Plant Project Report 2025: Detailed Setup, Machinery, and Market Insights

Introduction
A float glass manufacturing plant project report serves as a vital blueprint for establishing and operating a facility that produces flat glass, also known as float glass. Float glass is widely used in various industries, including construction, automotive, electronics, and interior design, due to its superior quality and flatness. The float glass process, pioneered by Sir Alastair Pilkington in the 1950s, revolutionized glass production by creating a smoother, more uniform product. This report will cover essential aspects of setting up a float glass manufacturing plant, such as market analysis, raw materials, production techniques, and financial planning.
Market Overview and Analysis
The float glass market has seen significant growth, driven by the booming construction and automotive sectors. With urbanization, industrialization, and increasing demand for high-quality glass in residential, commercial, and industrial buildings, the global demand for float glass is expected to continue rising. Additionally, as energy efficiency becomes more important in building designs, energy-efficient glass, such as low-emissivity (Low-E) glass, has become increasingly popular, further boosting market growth.
Key factors driving market demand include:
-
Construction Industry: Float glass is extensively used in windows, facades, and glazing applications, making it a critical component in residential, commercial, and industrial construction projects.
-
Automotive Industry: The increasing demand for vehicles, particularly those with energy-efficient and advanced glass features, like solar control glass and laminated glass, has contributed to the growth of the float glass market.
-
Interior Design: The growing trend of using glass in home décor, including furniture, partitions, and decorative elements, has spurred the demand for float glass products.
-
Technological Advancements: The introduction of advanced glass coatings, tinted glass, and safety glass products has opened new opportunities in both construction and automotive markets.
In addition to these sectors, float glass is also used in solar panels, electronics, and furniture manufacturing, all of which contribute to the market’s overall expansion.
Get a Free Sample Report with Table of Contents@
Raw Materials for Float Glass Production
The production of float glass requires specific raw materials, which must be sourced carefully for optimal quality and cost-effectiveness. The main ingredients in float glass production include:
-
Silica Sand (SiO2): The primary component of glass, silica sand provides the bulk of the raw material required for the glass-making process.
-
Soda Ash (Na2CO3): Soda ash is used to lower the melting point of silica sand, enabling the creation of glass at a more energy-efficient temperature.
-
Limestone (CaCO3): Limestone is added to stabilize the glass and improve its durability and chemical properties.
-
Alumina (Al2O3): Alumina is added to improve the glass's resistance to thermal shock and enhance its overall strength.
-
Other Additives: These may include magnesium oxide, barium oxide, and iron oxide, which can be used to modify the properties of the glass, such as its color, strength, and clarity. Additives such as coloring agents and chemicals for special glass properties (e.g., UV filtering) are also used for specific applications.
-
Recycled Glass (Cullet): Recycled glass is a crucial component of float glass production. It reduces the need for raw materials, lowers energy consumption, and supports environmental sustainability.
Float Glass Manufacturing Process
The production of float glass follows a well-established and efficient process. The most common method used today is the float glass process, which involves the following key steps:
1. Batching and Mixing
The raw materials (silica sand, soda ash, limestone, alumina, and other additives) are carefully measured and mixed to create a uniform batch of glass.
2. Melting
The raw material batch is transferred to a furnace, where it is heated to temperatures of about 1,600 to 1,700°C (2,912 to 3,092°F). This high temperature melts the raw materials into a molten glass.
3. Float Process
Once the raw material has melted, the molten glass is poured onto a bath of molten tin. The glass floats on the tin, which provides a perfectly flat surface, ensuring uniform thickness and smoothness. This is the core of the float glass process, which gives the glass its name. The glass spreads and adjusts to the desired thickness based on the speed and flow of the molten tin.
4. Cooling
The molten glass is gradually cooled in a controlled manner, allowing it to solidify without developing stress fractures. The cooling process takes place in a lehr, a long chamber where the glass is slowly cooled to ambient temperature.
5. Cutting
Once the glass has cooled and solidified, it is cut into the required sizes and shapes. Automated cutting machines are used to slice the glass into sheets of various dimensions, which are then carefully packaged for transportation.
6. Finishing
In some cases, additional processes such as polishing, coating, or laminating are performed on the glass to enhance its properties, like providing UV protection, safety features, or aesthetic appeal.
7. Quality Control
Throughout the production process, stringent quality control measures are implemented to ensure that the glass meets the required specifications for clarity, strength, thickness, and overall quality. Tests are conducted on surface quality, dimensions, and any defects like bubbles or cracks.
Types of Float Glass Products
Float glass can be tailored to meet specific requirements by adjusting its properties during production. Some common types of float glass include:
-
Clear Glass: Standard float glass used for windows, glass facades, and general architectural purposes. It provides excellent transparency and uniformity.
-
Low-E Glass: Glass with a thin, transparent coating that reflects heat while allowing visible light to pass through. This type of glass is used in energy-efficient buildings and windows to reduce heating and cooling costs.
-
Tinted Glass: Glass that is treated with metal oxide coatings or coloring agents to reduce glare and heat transfer. Tinted glass is popular in automotive windows and building applications.
-
Laminated Glass: Glass that is bonded together with a plastic layer to enhance safety. It is commonly used in automotive windshields, as well as in buildings to prevent shattering.
-
Tempered Glass: Heat-treated glass that is stronger and safer than regular float glass. It is often used in doors, shower panels, and glass furniture.
-
Reflective Glass: Glass with a reflective coating that improves heat insulation and aesthetic appeal. It is commonly used in commercial and high-rise buildings.
-
Solar Control Glass: Specially coated glass designed to reduce solar heat gain and protect interiors from UV radiation. This type of glass is widely used in energy-efficient building designs.
Investment and Financial Planning
The capital investment required to establish a float glass manufacturing plant is considerable. Major expenses typically include:
-
Land Acquisition: A large tract of land is needed for the plant, storage areas, and raw material handling.
-
Machinery and Equipment: The plant requires specialized machinery for melting, floating, cooling, cutting, and finishing glass. Additionally, furnaces, lehrs, and quality control equipment are significant investments.
-
Raw Materials: Initial stockpiles of raw materials, including silica sand, soda ash, and limestone, are needed to begin production.
-
Labor Costs: Skilled workers, engineers, and technicians are required to operate the plant efficiently.
-
Energy Consumption: Glass production is an energy-intensive process, requiring a consistent and reliable energy supply. The cost of energy will be a significant ongoing operational expense.
-
Regulatory Compliance and Permits: Environmental regulations related to air quality, waste management, and emissions must be complied with, requiring investment in pollution control measures and permits.
-
Marketing and Distribution: The cost of establishing a distribution network and marketing the product to target customers (construction companies, automotive manufacturers, glass distributors) is also an essential part of the financial planning process.
Despite the large initial capital investment, float glass manufacturing can be highly profitable, particularly in areas with significant construction and automotive industries. Moreover, modern advancements in energy-efficient glass and environmentally friendly practices provide opportunities for long-term growth.
Challenges and Risk Factors
Starting a float glass manufacturing plant comes with several challenges and risks:
-
High Energy Consumption: Glass production requires substantial energy, which can lead to high operating costs, especially if energy prices are volatile.
-
Raw Material Price Fluctuations: The prices of raw materials like silica sand and soda ash can fluctuate due to market demand and supply chain disruptions.
-
Environmental Concerns: The manufacturing process can result in emissions, waste, and energy consumption, requiring compliance with strict environmental regulations.
-
Competition: The float glass industry is competitive, with several established players. New entrants must differentiate their products through innovation, quality, or pricing to gain a foothold in the market.
-
Technological Advancements: The float glass industry is continually evolving with new technology. Investment in research and development is essential to stay competitive and meet the growing demand for specialized glass products.
Media Contact
Company Name: Claight Corporation
Contact Person: Lewis Fernandas, Corporate Sales Specialist — U.S.A.
Email: sales@expertmarketresearch.com
Toll Free Number: +1–415–325–5166 | +44–702–402–5790
Address: 30 North Gould Street, Sheridan, WY 82801, USA
Website: www.expertmarketresearch.com
Aus Site: https://www.expertmarketresearch.com.au
What's Your Reaction?
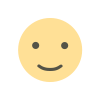





