How Can Oil Condition Monitoring Revolutionize Equipment Maintenance?
Discover how Oil Condition Monitoring is enhancing equipment performance, reducing downtime, and lowering maintenance costs in industries globally.
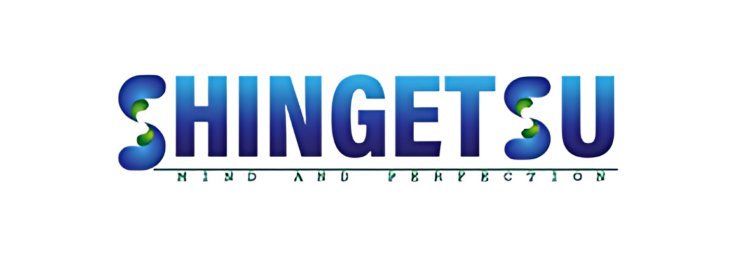
Introduction:
How can you avoid costly machinery breakdowns and improve the longevity of your equipment? The answer lies in Oil Condition Monitoring. This advanced system allows real-time tracking of oil properties, ensuring your machinery operates at its peak performance while saving you money on repairs and downtime. Let's explore the growing Oil Condition Monitoring Market and why this technology is becoming a game-changer in various industries.
What Is Oil Condition Monitoring?
Oil Condition Monitoring (OCM) is a process used to assess the condition of lubricants in machinery. By tracking factors like oil temperature, viscosity, and contamination levels, OCM helps identify potential issues before they lead to failures. This technology is widely used in industries such as automotive, manufacturing, and energy to keep machinery running efficiently.
In essence, Oil Condition Monitoring enables real-time analysis of lubricants, which aids in predicting equipment failures. It ensures that oil used in engines, compressors, and other systems performs optimally for longer periods, preventing expensive repairs or replacements.
How Does Oil Condition Monitoring Work?
Oil Condition Monitoring involves the use of sensors, controllers, and software that continuously track the condition of oils in various machinery. These systems monitor key parameters, such as:
- Viscosity: Ensures the oil maintains proper thickness, which is crucial for lubrication efficiency.
- Temperature: Detects overheating, a common cause of lubricant degradation.
- Contaminants: Identifies foreign particles that could damage machinery.
- Water Content: Tracks water dilution in oil, which can impact lubrication performance.
Through continuous monitoring, these systems can predict when the oil will need to be replaced or when mechanical issues may arise, allowing maintenance teams to address problems early.
The Growth of the Oil Condition Monitoring Market
The Oil Condition Monitoring Market is experiencing rapid growth due to several key factors. The increasing demand for cost-effective and reliable maintenance solutions is driving the adoption of oil monitoring systems. Additionally, industries are looking to optimize machine uptime, reduce oil wastage, and cut down on maintenance costs, making oil condition monitoring a must-have technology.
The market is also benefitting from advancements in Internet of Things (IoT) and Industry 4.0 technologies. These innovations have made it easier for industries to integrate real-time monitoring into their operations, providing immediate insights and enabling faster decision-making.
Key Drivers of Oil Condition Monitoring Adoption
-
Cost-Effectiveness: Regular oil changes and unplanned downtime can be costly. By using oil condition monitoring, businesses can extend oil change intervals and reduce maintenance costs.
-
Increased Equipment Lifespan: By ensuring that oil remains in optimal condition, machinery can run longer without major repairs, ultimately saving money and reducing the need for replacements.
-
Real-Time Monitoring: The ability to monitor oil condition in real time allows operators to detect small issues before they become significant problems, minimizing the risk of costly failures.
-
Environmental Benefits: With the rise of environmental concerns, using oil condition monitoring helps minimize oil waste and optimize lubricant usage, which is a sustainable practice in many industries.
Segment Analysis: On-Site vs. Off-Site Oil Condition Monitoring
There are two main types of oil condition monitoring: on-site and off-site.
-
On-Site Monitoring: This type is beneficial for industries that require continuous, real-time data. On-site monitoring allows companies to track oil condition directly at the equipment location, offering immediate feedback. It helps reduce downtime, enhance productivity, and minimize oil waste. As a result, the on-site segment has captured a significant share of the Oil Condition Monitoring Market.
-
Off-Site Monitoring: In this setup, oil samples are sent to a lab for analysis. Although this approach takes longer, it provides more in-depth insights into the oil's condition. Off-site monitoring systems are typically used when continuous real-time data isn't necessary, but detailed analysis is required.
Both methods play a crucial role in improving the maintenance processes of machinery and equipment.
Applications of Oil Condition Monitoring
Oil Condition Monitoring is widely applied across several industries, each with its unique needs. Some key applications include:
- Automotive Industry: Real-time oil monitoring helps extend engine life and optimize fuel efficiency in vehicles.
- Power Generation: Monitoring the oil in turbines, engines, and compressors ensures reliable performance and prevents catastrophic failures in power plants.
- Industrial Manufacturing: Oil condition monitoring is essential for keeping equipment like gear systems, hydraulic systems, and machines running smoothly.
- Marine: In shipping and marine transportation, oil monitoring systems ensure the engines and other machinery operate efficiently, even in the harshest conditions.
As the market grows, more industries are adopting oil condition monitoring as a standard maintenance practice.
Oil Condition Monitoring in Key End-User Industries
-
Transportation: The transportation sector, including automobiles, aerospace, and heavy vehicles, is expected to dominate the Oil Condition Monitoring Market by 2027. Oil condition monitoring systems help manage wear and tear on vehicle components, reducing the risk of breakdowns and extending vehicle life.
-
Oil & Gas: In the oil and gas industry, machinery operates under high pressure and extreme conditions. Monitoring the condition of lubricants ensures that equipment continues to operate without failure, improving safety and efficiency.
-
Power Generation: Power generation relies on turbines and engines, which require constant maintenance. Oil condition monitoring helps prevent failures in these critical systems, ensuring that power plants run smoothly.
-
Mining: Heavy machinery used in mining operations is subject to extreme wear. By monitoring the condition of lubricants, mining companies can reduce unplanned downtime and improve equipment performance.
Regional Analysis of the Oil Condition Monitoring Market
The Oil Condition Monitoring Market is segmented geographically into regions such as North America, Europe, Asia Pacific, South America, and the Middle East & Africa. Among these, North America is expected to dominate the market by 2027. The region has a strong presence of key players and a growing demand for oil condition monitoring across various industries.
- Europe is also witnessing significant growth due to the increasing focus on industrial efficiency and regulatory pressure to adopt sustainable practices.
- Asia Pacific will experience rapid growth due to industrialization and the rising demand for efficient machinery management in countries like China and India.
As the market expands, more regions will adopt oil condition monitoring technologies to boost productivity and reduce operational costs.
Challenges in the Oil Condition Monitoring Market
While oil condition monitoring offers numerous benefits, there are challenges associated with its adoption. Some of the key challenges include:
- High Initial Investment: Setting up real-time oil condition monitoring systems can be expensive, particularly for small and medium-sized enterprises (SMEs).
- Complexity of Integration: Integrating oil condition monitoring into existing machinery and systems can be complex, especially in older equipment.
- Data Overload: With continuous monitoring comes an influx of data. Managing and interpreting this data can be overwhelming without proper analytics tools and expertise.
However, as technology advances and becomes more affordable, these challenges are expected to diminish.
The Future of the Oil Condition Monitoring Market
The future of the Oil Condition Monitoring Market looks promising. As industries continue to focus on efficiency, sustainability, and cost savings, the demand for real-time monitoring solutions will increase. With advancements in IoT, artificial intelligence, and machine learning, oil condition monitoring systems will become even more intelligent, capable of predicting failures and optimizing performance in real time.
Conclusion
Oil Condition Monitoring is revolutionizing maintenance practices across industries, offering significant cost savings, increased equipment longevity, and improved operational efficiency. As more businesses recognize its value, the Oil Condition Monitoring Market will continue to expand, driving innovations that will make machinery maintenance smarter, faster, and more efficient.
To learn more about how Oil Condition Monitoring can benefit your operations, visit the detailed analysis on the Oil Condition Monitoring Market.
What's Your Reaction?
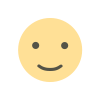





