Maximize Accuracy: How a Tool Presetter Enhances CNC Performance!
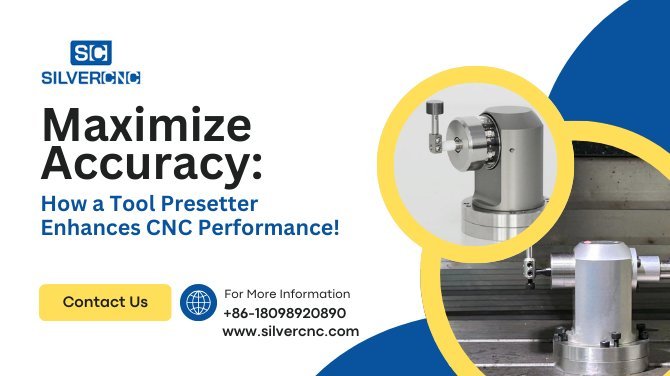
What is a Tool Presetter?
A tool presetter is a precision device used in CNC operations to measure the dimensions and offsets of cutting tools before they are mounted on the CNC machine. The tool presetter allows operators to set tools accurately outside the machine, reducing setup time and ensuring that the tools are correctly aligned with the machine's coordinate system. This equipment is essential for maintaining consistent quality in machining and ensuring minimal downtime during production.
Why Tool Presetters Matter in CNC Operations
Tool presetters matter because they provide the level of precision needed for high-quality machining. CNC machines rely on accurate tool positioning to create complex shapes and parts. A tool presetter eliminates human error, speeds up the process, and increases the overall efficiency of operations.
The Role of Precision in CNC Machining
Importance of Precision in CNC Work
Precision is the backbone of CNC machining. The slightest error in tool alignment or measurement can result in a defect that is costly to repair. CNC machining is typically used to manufacture parts that require tight tolerances—meaning even a small discrepancy can lead to failure. The role of a tool presetter here is to ensure that every tool is calibrated to its correct dimensions before it even touches the workpiece.
Common Challenges in CNC Machining
Some of the challenges that manufacturers face include long setup times, tool wear, and inaccurate measurements. These challenges can lead to inconsistent results, production delays, and even machine damage. A tool presetter helps mitigate these issues by allowing for faster, more accurate tool measurement and reducing the likelihood of errors that could impact the machining process.
How a Tool Presetter Enhances CNC Performance
Accurate Tool Measurement
The primary function of a tool presetter is to measure tools with great precision. This ensures that the tool is correctly aligned and ready for operation. When tools are measured outside the CNC machine, operators can catch issues like wear, incorrect tool lengths, or damaged tips, all of which would have otherwise gone unnoticed and affected the workpiece.
Minimizing Tool Setup Time
Tool setup time is one of the most significant factors influencing production efficiency. By using a tool presetter, operators can set tools faster, minimizing downtime. This is particularly beneficial for shops that handle high-volume production, where every second counts. With a tool presetter, operators can quickly measure and adjust tools, so they are always ready for use without the need for remeasurement within the machine.
Improving Consistency Across Production Runs
A tool presetter ensures that tools are set up the same way every time. This leads to greater consistency across production runs. Whether you're machining a single part or running a batch, the ability to maintain consistent tool offsets and measurements helps produce identical parts with the same level of quality.
Key Benefits of Using a Tool Presetter
Boosting Productivity and Efficiency
When tools are set up more efficiently, it leads to a direct boost in productivity. Operators spend less time adjusting tools during production and more time actually machining. With a tool presetter, you can achieve higher throughput and faster turnaround times, which is crucial for meeting tight deadlines and fulfilling customer orders.
Enhancing Tool Life and Reducing Wear
Another critical benefit of using a tool presetter is that it helps extend tool life. By ensuring tools are properly measured and aligned before use, the presetter reduces unnecessary wear and tear. Proper tool setup reduces the strain on the CNC machine and minimizes the need for frequent tool replacements, which leads to cost savings over time.
Reducing Machine Downtime
Machine downtime is expensive. Every minute that the CNC machine is not operating represents lost revenue. By using a tool presetter, you can reduce the time it takes to change or adjust tools, ensuring the machine runs longer and with less interruption. The more efficient your tool setup process is, the more time the CNC machine spends performing tasks rather than waiting for adjustments.
Enhancing Safety in the Workshop
Safety is always a concern in any machining environment. Improper tool alignment or miscalculation can lead to safety risks, such as accidents or machine damage. A tool presetter ensures that all tools are set with precise measurements, lowering the chances of misalignment that could cause accidents. Proper calibration and maintenance also reduce the risk of tool breakage and machine malfunctions.
Tool Presetter vs. Manual Setup
Comparison of Manual and Automated Tool Setting
Manual tool setting often involves guesswork, manual measurement, and adjustments while the tool is in the machine. This can result in inaccuracies, longer setup times, and increased risk of errors. A tool presetter, on the other hand, automates this process, ensuring precise measurements and consistent tool offsets every time.
Advantages of Using a Tool Presetter Over Manual Methods
Using a tool presetter offers several advantages over manual methods, including:
- Increased precision and accuracy.
- Faster setup times and quicker changeovers.
- Reduced potential for human error.
- Enhanced consistency across production runs.
How to Choose the Right Tool Presetter for Your CNC Needs
Considerations for Selecting a Tool Presetter
When choosing a tool presetter, there are several factors to consider, such as the type of CNC machine you use, the size of your tools, and the level of accuracy you require. You should also think about your shop's workflow—some presetters are designed for high-volume operations, while others are better suited for smaller, more specialized tasks.
Types of Tool Presetters Available
There are two main types of tool presetters: manual and automatic. Manual presetters require operators to input measurements, while automatic presetters do most of the work themselves. The choice depends on the complexity of your operations and the volume of tools you need to measure.
How to Match a Tool Presetter to Your CNC Machine
To ensure compatibility, it is essential to match your tool presetter with the specific CNC machine you use. Different machines have different tool holding systems and measuring requirements, so be sure to choose a presetter that can handle the size, weight, and type of tools you are using.
Maximizing ROI with a Tool Presetter
Long-term Cost Savings
While the initial investment in a tool presetter may seem significant, the long-term savings are undeniable. Reduced machine downtime, extended tool life, and increased production efficiency all contribute to a better return on investment. Over time, these savings will outweigh the upfront costs, making a tool presetter a valuable asset for any CNC shop.
Improving Workflow and Reducing Operator Fatigue
A tool presetter can streamline your workflow by automating a crucial part of the tool setup process. This not only saves time but also reduces operator fatigue. With less manual intervention, workers can focus on higher-level tasks, which improves both productivity and job satisfaction.
Real-World Examples of Tool Presetters in Action
Case Study: How a Tool Presetter Increased Efficiency
Many CNC shops have successfully integrated tool presetters into their operations. One such example is a high-volume manufacturing company that was able to reduce its tool setup time by 50% after implementing a tool presetter. This allowed the company to increase its output while maintaining the same level of quality, resulting in both time and cost savings.
Customer Testimonials and Success Stories
Customers across various industries, from aerospace to automotive, have praised the accuracy and efficiency of tool presetters. These testimonials underscore the significant benefits that come with implementing a tool presetter in CNC operations.
Maintenance Tips for Tool Presetters
Regular Calibration and Maintenance
To ensure that your tool presetter remains accurate over time, regular calibration and maintenance are necessary. This involves checking the accuracy of the device and making adjustments as needed. Following the manufacturer's maintenance recommendations will ensure that your presetter continues to perform at its best.
Keeping Your Tool Presetter in Optimal Condition
Proper storage and handling also play a role in extending the lifespan of your tool presetter. Avoid exposing it to harsh conditions or dropping it, and ensure that it's cleaned after every use.
The Future of Tool Presetters in CNC Machining
As technology advances, so does the role of tool presetters in CNC machining. In the future, tool presetters will likely become even more sophisticated, incorporating new technologies that will enhance their capabilities even further. A few tendencies to look out for are as follows:
Integration with AI and IoT
The future of tool presetters may include artificial intelligence (AI) and the Internet of Things (IoT) integration. AI could help presetters analyze tool wear and automatically adjust settings for optimal performance, while IoT technology could enable remote monitoring and diagnostics, allowing operators to track tool conditions in real time from anywhere.
Increased Automation
Increased automation in tool presetting will continue to enhance CNC machining efficiency. Fully automated systems could eliminate manual interventions altogether, allowing for faster and more precise measurements and tool changes. These automated systems would not only increase the speed of production but also reduce the risk of human error.
Smarter Calibration Systems
The future of tool presetters will also include smarter calibration systems that can automatically calibrate the tool presetter itself. This would reduce the need for regular manual calibration, ensuring that the system stays accurate and reducing downtime even further.
Improved User Interfaces
As user interfaces become more intuitive, tool presetters will become easier to use. Touchscreens, voice commands, and other user-friendly innovations will simplify the process of setting up and measuring tools. This ease of use will help operators spend less time on setup and more time on productive machining.
In summary, a tool presetter is no longer just a luxury; it is a vital tool for CNC operations aiming to stay competitive in today’s fast-paced manufacturing environment. With the ability to improve precision, reduce setup times, extend tool life, and enhance safety, a tool presetter can significantly optimize your production process.
As the industry continues to evolve, so too will the role of tool presetters. With advancements in AI, automation, and IoT, these devices will become even more powerful tools, driving the next generation of manufacturing efficiency. If you’re serious about staying ahead in CNC machining, investing in a tool presetter is a strategic move that will yield both immediate and long-term benefits.
FAQs
- What is the main advantage of using a tool presetter in CNC machining?
A tool presetter enhances precision, reduces setup times, and minimizes errors in CNC machining, leading to improved productivity and consistency in production.
- How does a tool presetter contribute to better tool life?
By ensuring tools are properly aligned and measured before use, a tool presetter reduces unnecessary wear and tear on tools, thus extending their lifespan.
- Can a tool presetter help reduce downtime in CNC operations?
Yes, a tool presetter minimizes downtime by speeding up tool changes and setup processes, allowing machines to remain operational for longer periods.
- How do I choose the right tool presetter for my CNC machine?
Consider factors such as your CNC machine’s specifications, the types of tools you use, your production volume, and the level of precision required when selecting a tool presetter.
- Are there any maintenance tips to ensure the longevity of a tool presetter?
Regular calibration, cleaning, and proper handling of the tool presetter can ensure its accuracy and longevity. It's also crucial to adhere to the manufacturer's maintenance recommendations.
What's Your Reaction?
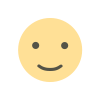





