Tips for Selecting the Best Pressing Die Set for Your Application
Selecting the right pressing die set ensures efficiency, precision, and durability in various industrial and research processes.
A pressing die set is a crucial component in manufacturing and laboratory applications, used for shaping, compressing, and forming materials under high pressure. Selecting the right pressing die set ensures efficiency, precision, and durability in various industrial and research processes.
Key Factors to Consider When Choosing a Pressing Die Set
1. Material Compatibility
The material of the pressing die set should be compatible with the materials being processed. Common materials include:
Hardened steel: Suitable for metal forming and high-strength applications.
Tungsten carbide: Ideal for high-pressure and wear-resistant applications.
Stainless steel: Best for corrosion-resistant environments.
2. Die Set Size and Shape
Choosing the appropriate die size and shape ensures that the final product meets design specifications. Factors to consider include:
Diameter and thickness of the die cavity
Shape requirements (cylindrical, rectangular, custom shapes)
Tolerance levels for precision applications
3. Pressure Capacity
The pressing die set must be capable of withstanding the required pressure for your application. Overloading can lead to material deformation or failure. Ensure that the die set matches the specifications of your hydraulic or mechanical press.
4. Surface Finish and Coatings
A smooth surface finish reduces friction and enhances durability. Consider coatings such as:
Titanium nitride (TiN): Improves hardness and wear resistance.
Diamond-like carbon (DLC): Reduces friction and extends lifespan.
Ceramic coatings: Enhance thermal and chemical resistance.
5. Durability and Maintenance Requirements
Investing in a high-quality pressing die set minimizes maintenance and replacement costs. Key factors to ensure durability include:
Heat-treated materials for enhanced strength
Regular lubrication and cleaning
Proper storage to prevent corrosion and damage
6. Customization Options
For specialized applications, custom die sets may be required. Manufacturers offer:
Custom dimensions and geometries
Specialized coatings and surface treatments
Enhanced load-bearing capacities
7. Compatibility with Pressing Equipment
Ensure the die set is compatible with your existing pressing equipment, including:
Manual, hydraulic, or pneumatic presses
Automatic or semi-automatic pressing systems
Temperature-controlled pressing units
Applications of Pressing Die Sets
1. Powder Metallurgy
Used for compacting metal powders into precise shapes before sintering.
2. Pharmaceutical Industry
Essential for tablet and pill formation, ensuring uniformity and dosage accuracy.
3. Ceramic and Composite Material Processing
Used for creating high-strength ceramics and composite materials with consistent density.
4. Automotive and Aerospace Industries
Employed in metal forming and component manufacturing for high-performance applications.
5. Research and Laboratory Applications
Used in material science, chemistry, and physics experiments requiring precise pressure conditions.
Conclusion
Selecting the best pressing die set depends on factors such as material compatibility, pressure capacity, surface finish, durability, and customization options. Investing in the right die set enhances efficiency, precision, and longevity in both industrial and research applications.
What's Your Reaction?
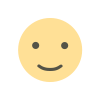





