What are the benefits of using a sheet metal laser cutter for industrial and commercial applications
Sheet metal laser cutters have become an essential tool in industrial and commercial applications due to their high precision, speed, and efficiency.

Sheet metal laser cutters have become an essential tool in industrial and commercial applications due to their high precision, speed, and efficiency. Whether in automotive manufacturing, aerospace engineering, construction, or electronics production, laser cutting technology offers significant advantages over traditional cutting methods. Below, we explore the key benefits of using a sheet metal laser cutter and how it enhances manufacturing processes.
1. High Precision and Accuracy
One of the primary advantages of a sheet metal laser cutter is its ability to deliver precise and accurate cuts. With cutting tolerances as tight as ±0.01mm, laser cutting ensures clean edges, intricate designs, and minimal material wastage. This level of precision is crucial in industries where even a small error can lead to defective products or assembly issues.
2. Fast Cutting Speed and Efficiency
Compared to traditional cutting methods such as mechanical shearing or plasma cutting, laser cutting is significantly faster. Modern sheet metal laser cutters can operate at high speeds, reducing production time and increasing output. This is especially beneficial for large-scale manufacturing, where time efficiency directly impacts profitability.
3. Versatility in Material and Thickness
A sheet metal laser cutter is capable of cutting various metals, including:
- Stainless steel
- Mild steel
- Aluminum
- Copper
- Brass
Additionally, laser cutters can handle a range of thicknesses, from thin sheets (as low as 0.5mm) to thick metal plates (up to 25mm, depending on laser power). This versatility makes them suitable for diverse applications across multiple industries.
4. Minimal Material Waste
Traditional cutting methods often lead to material wastage due to rough edges, imprecise cuts, and larger kerf widths. Sheet metal laser cutters, on the other hand, produce clean cuts with minimal kerf width, optimizing material usage. This not only reduces costs but also supports sustainable manufacturing practices by minimizing waste.
5. Non-Contact Cutting Process
Unlike mechanical cutting methods that involve physical contact between the cutting tool and the material, laser cutting is a non-contact process. The laser beam does not exert any force on the sheet metal, reducing the risk of deformation, warping, or mechanical wear. This is particularly advantageous for thin or delicate metal sheets that require precision without damage.
6. Automation and Integration with CNC Systems
Modern sheet metal laser cutters are integrated with CNC (Computer Numerical Control) systems, allowing automated and programmable cutting processes. CNC-controlled laser cutting offers consistency, repeatability, and error-free execution, making it ideal for mass production. Additionally, integration with CAD/CAM software enables seamless design-to-production workflows.
7. Cost-Effective in the Long Run
While the initial investment in a sheet metal laser cutter may be higher than traditional cutting tools, the long-term savings make it a cost-effective solution. Factors such as reduced material waste, lower maintenance costs, and higher productivity contribute to significant cost savings over time. Additionally, automation reduces labor costs, further improving profitability.
8. Reduced Post-Processing Requirements
Laser cutting produces smooth and burr-free edges, eliminating the need for extensive post-processing such as grinding or polishing. This saves time and labor costs, making the entire production process more efficient.
9. Safe and Environmentally Friendly
Laser cutting is a safer alternative to conventional cutting methods since it does not require physical contact with sharp tools or blades. Additionally, it generates less noise and dust, creating a cleaner and safer work environment. With minimal material waste and energy-efficient operations, laser cutting is also an eco-friendly option for manufacturers.
Conclusion
Sheet metal laser cutters have transformed industrial and commercial manufacturing by offering high precision, speed, and efficiency. Their ability to cut various metals with minimal waste, reduced maintenance costs, and automation capabilities makes them a superior choice over traditional cutting methods. As industries continue to demand higher quality and efficiency, sheet metal laser cutting will remain a crucial technology for businesses aiming to improve production processes and reduce operational costs.
What's Your Reaction?
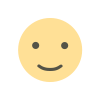





